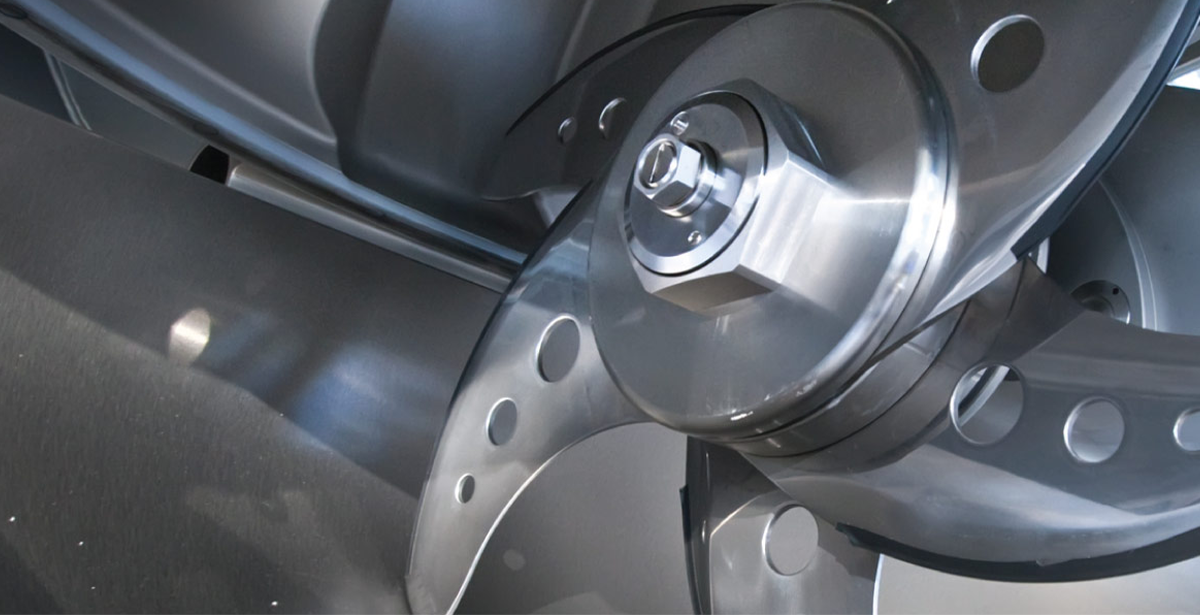
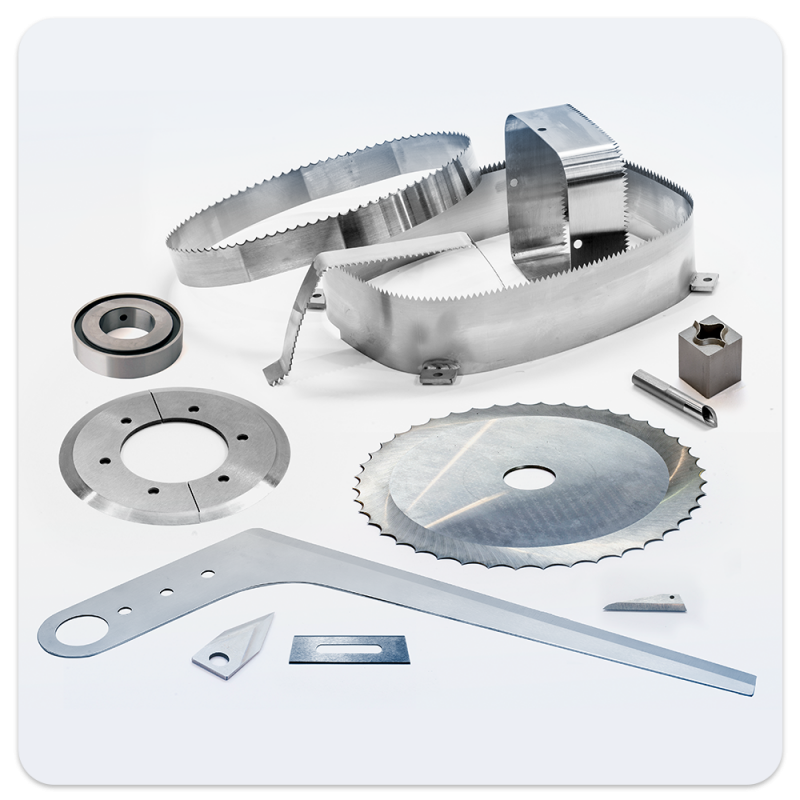
Experience You Can Trust
Quality. Delivered.
We boast a unique array of dedicated machines and manufacturing cells to meet the consistent demand of our dynamic customers’ needs with quick turnaround. Our products are carefully crafted under strict quality control using OEM specifications. Most of our knives are available in stock, with high quality materials selected to prolong the life and performance of the product. Our vast inventory allows for same-day shipping on a large variety of standard knives and products.
Frequently Asked Questions
Upgrade your material, wear coatings, and/or surface treatments. Other performance changes can be found with revising your edge detailing, inlaying carbide or solid carbide. Cryogenic processing is always an option too. There are a number of ways to improve production performance, including material upgrades, wear coatings, cryogenic treatments, and/or surface treatments. Edge geometry modifications are another area to explore, as well, to improve production performance.
Reduced lead times means increased machine capacity. Reduced lead times mean you get your product faster, and that in turn means you can reduce the stock you keep on your shelves to keep your operation running.
Yes, we offer vendor managed stocking programs. Ask your sales representative today if this applies to you.
We offer nonstick coatings, which reduces buildup. We have a selection of non-stick coatings available that may reduce film build-up on your knives. Give us a call today to discuss your options further.
No. We have the largest print archive in the industry for packaging, food processing, converting, and print. We have over 70,000 prints accumulated since our inception in 1908. We can also reverse engineer and replicate any knife or blade in the market. We have an in-house spectrometer, optical comparator, and precision inspection equipment, to name a few of our tools for identifying knives.
Yes! We can laser etch logos, part numbers, websites, phone numbers, OEM names – just about anything you might want on your knives to help with identification.
Bevels- center holes- slotted teeth-100” toothed splicer blades- 18” diameter circulars-77” precision ground tray strip stock ( 50-100 variations- tooth pitch- width- thickness)- edge detail- beveled only, scalloped- serrated- micro denture- saw tooth- tear notch knives
We do have size limitations on the knives we manufacture, and these do vary by product type. A few examples are 18” diameter for circular knives, and 77” length for precision-ground strip stock. Most knives in the market are within our manufacturing parameters.
We recommend tool steels with a service life compared to 52100 1X, D-2 3X , M-2 4X, 440 3X, powdered metal 8X, carbide 10X. Wear resistance, corrosion resistance, and toughness should be considered when considering materials or coatings. We offer a variety of materials, including carbon steels, stainless steels, tool steels, die steels and high speed steels. Whatever steel your knives are made from, the odds are we stock it and can manufacture what you need.
We have 3 manufacturing facilities to accommodate competitive pricing, purchasing of low volume quantities, and quick delivery. Our plants are in Pennsylvania, USA, Sheffield, England, and Indore, India.
Standard lead time can vary by product type.Over 50% of our annual sales are stock and ship off the shelf.For make to order items, lead times are typically 4 to 6 weeks, but can be longer – please check with our sales team for an accurate lead time for your specific item.
Pricing is often influenced by volume – the more pieces we can run in a batch, typically the lower our production costs are. We do offer volume price breaks, and we also have a robust blanket order process available to help you take advantage of volume pricing.